Skin-Friendly Synthetic Leather for Greener Consumer Electronics for the Metaverse
Aging Resistant Silicone Alternative to PU and other Faux Leathers
Hsinchu, Taiwan, November 19, 2021 - Experienced silicone product manufacturer General Silicones (GS) releases today its VL301 Silicone Velvet Leather. The soft, velvet-like touch makes the leather material ideal for consumer electronics like headsets, AR/VR glasses and gloves for the metaverse, and other consumer electronics that often get exposed to the wearer's skin.
Anti-Allergic Skin Friendly Material
Electronic manufacturers currently rely on PU-based faux leather, which can create allergic reactions for some users during prolonged use. The VL301 Silicone Velvet leather is made from silicone. Silicone is well-known for its non-allergenic properties and is preferred for baby products. GS has manufactured silicone products for over 50 years and supplies silicone products for the infant, toys, and healthcare industry.
Long-Lasting Synthetic Leather that does not Crack and Decolorize
PU leather commonly used in consumer electronics cracks and becomes sticky from natural oils at skin and hair contact areas. Sweat and humidity adds to this effect by additionally degrading the PU material, leading to decolorization. On the other hand, silicone is an inert material that neither reacts to oils nor cleaning products like detergents or alcohol. Silicone is also UV-resistant. It does not age, discolor or crack under direct sunlight.
A Green Vegan Leather Alternative to PU Leather
The vegan leather of GS brand is manufactured using silicone. The raw material is extracted from silica, which is the main component of sand. Studies have shown that pure silicone carries no harmful consequences on nature or humans. This material is both durable, recyclable, and harmless. The carbon footprint of silicone products is low as silicone products reduce more carbon dioxide emissions during their lifetime than created during the manufacturing process.
Supporting COP26 targets by Reducing Electronic Waste Creation
Consumer electronics such as headsets are often discarded not due to failing electronics but due to the damages in the device's looks from cracking and decolorizing leather. Manufacturers can prevent the creation of unnecessary electronic waste by extending product life by using silicone leather. Customer satisfaction will be increased, and the brands' image for quality will be sustained for the product's entire lifetime.
Patented Innovation for Silicone Printability and Adhesion
The patented Compo-SiL® technology of GS resolves two key elements that have prevented the widespread use of silicone leather so far. Compo-SiL® technology allows strong and lasting bonding of silicone leather to textiles, metals, and other base materials using standard industrial adhesives commonly used in mass production. Even roll-to-roll mass production of silicone leather is possible with Compo-SiL® leather.
Digital printing of the base surface of Compo-SiL® leather allows manufacturers to print logos and decorative prints. The prints are protected from environmental damage and wear by the silicone cover sheet, allowing brands to experiment with the material for increased individualization and artistic expression of their final product.
Sourcing managers and manufacturers interested in more information on Compo-SiL® silicone leather can contact General Silicones at compo-sil@gsweb.com.tw.
About General Silicones
General Silicones (GS) was founded in 1970 in Taipei, Taiwan, and is now represented worldwide – including Europe, China, Japan, and South-East Asian countries. GS is a major distributor of silicone materials and an active silicone products manufacturer with ISO 9001, IATF 16949, and ISO 14001 certifications. The company has manufacturing plants in Hsinchu, Taiwan; Wujiang, China; and Bac Giang, Vietnam. With decades of experience in this field, GS has the ability and capacity to provide a wide range of silicone products for many industries, including medical, automobile, consumer products, electronics, and IT. For more information about GS, please visit www.generalsilicones.com. For more information on Compo-SiL®, please visit www.compo-sil.com
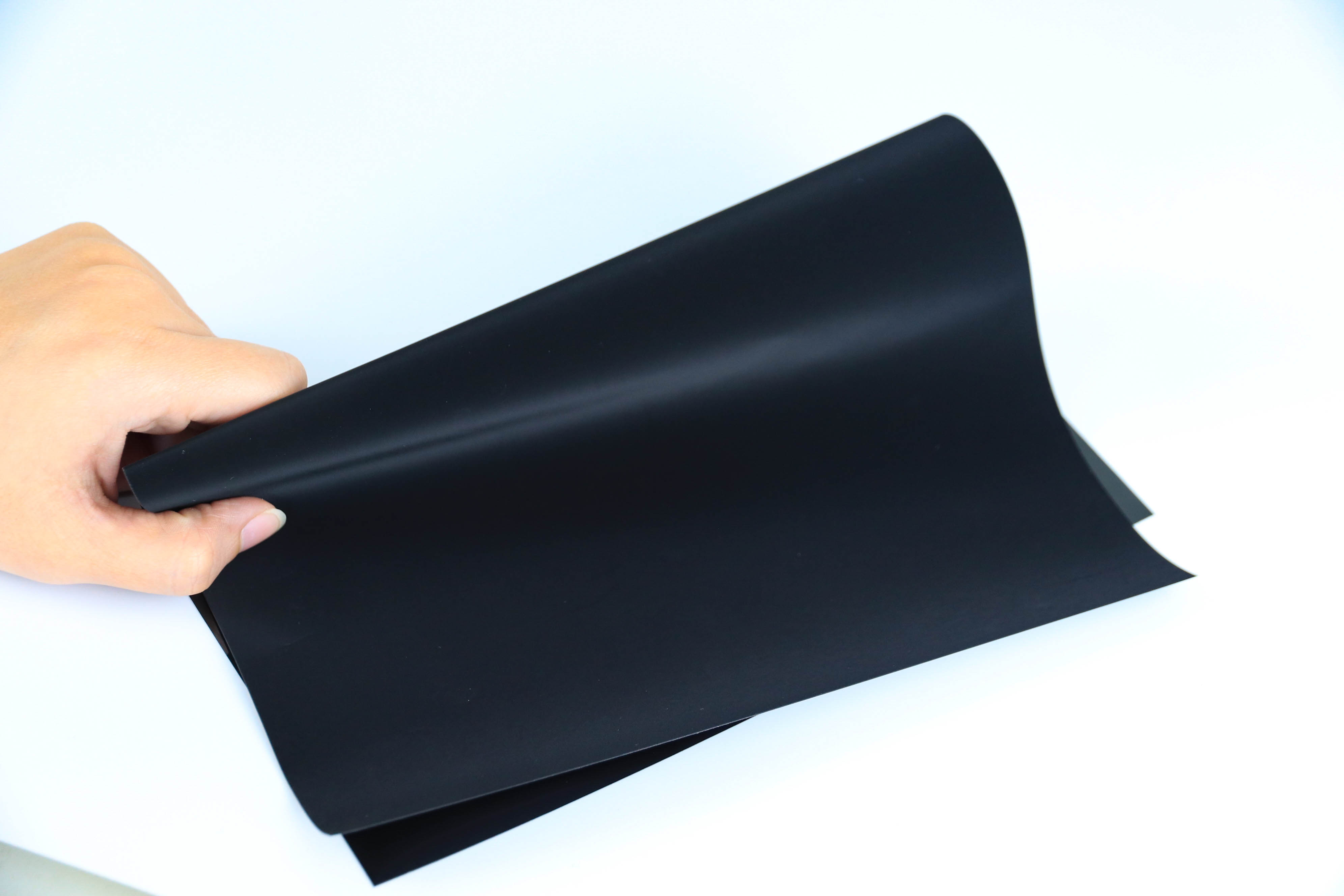
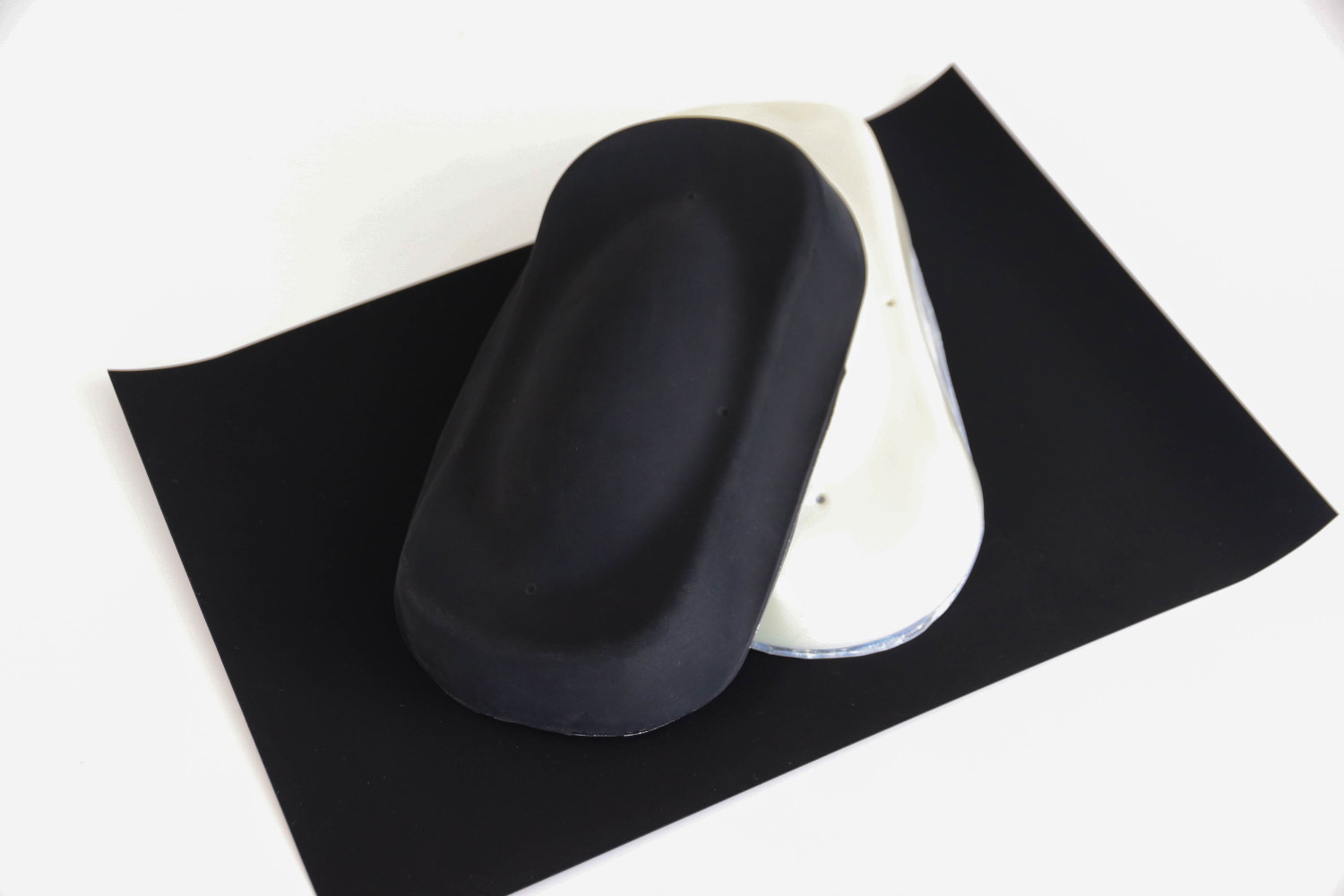
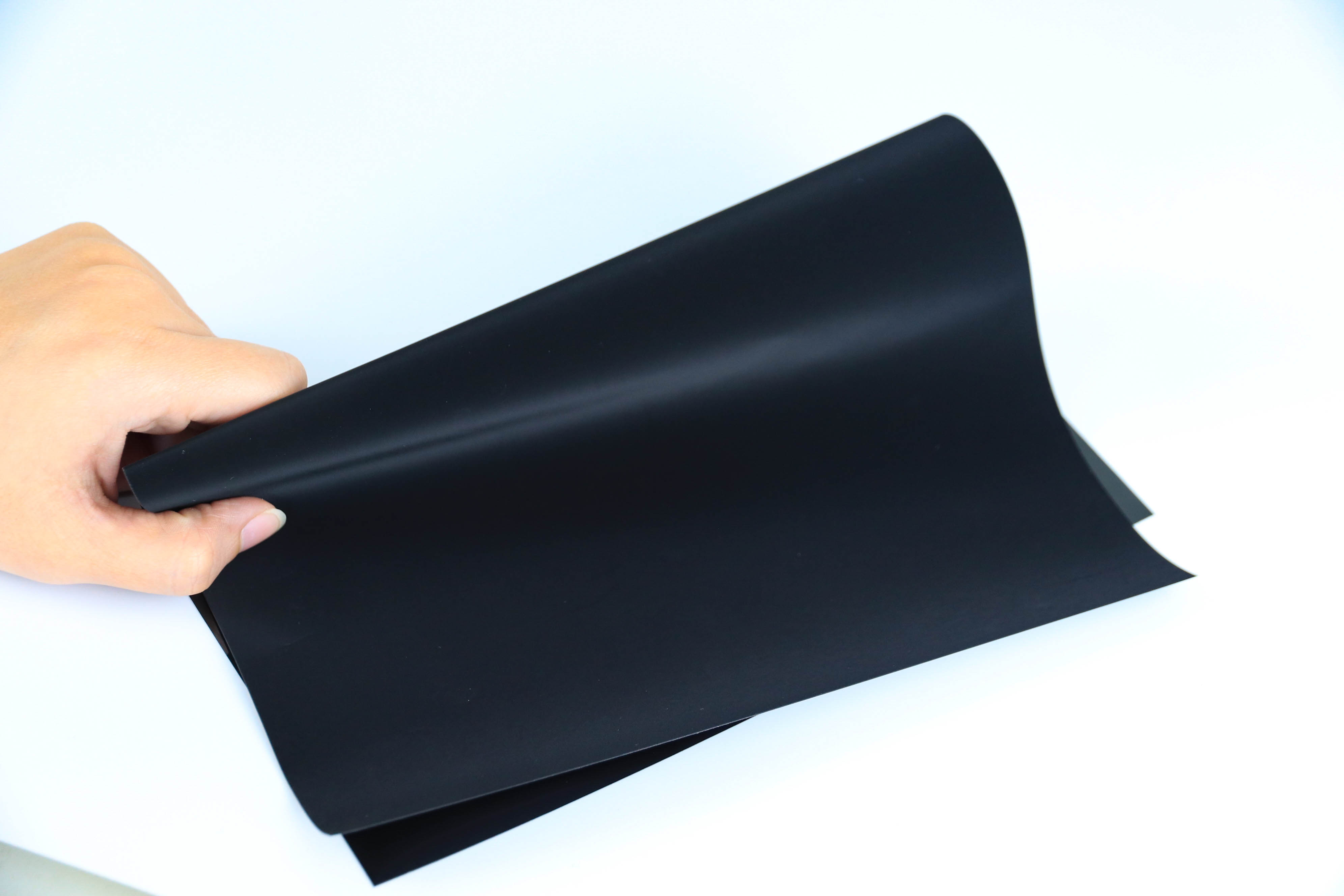
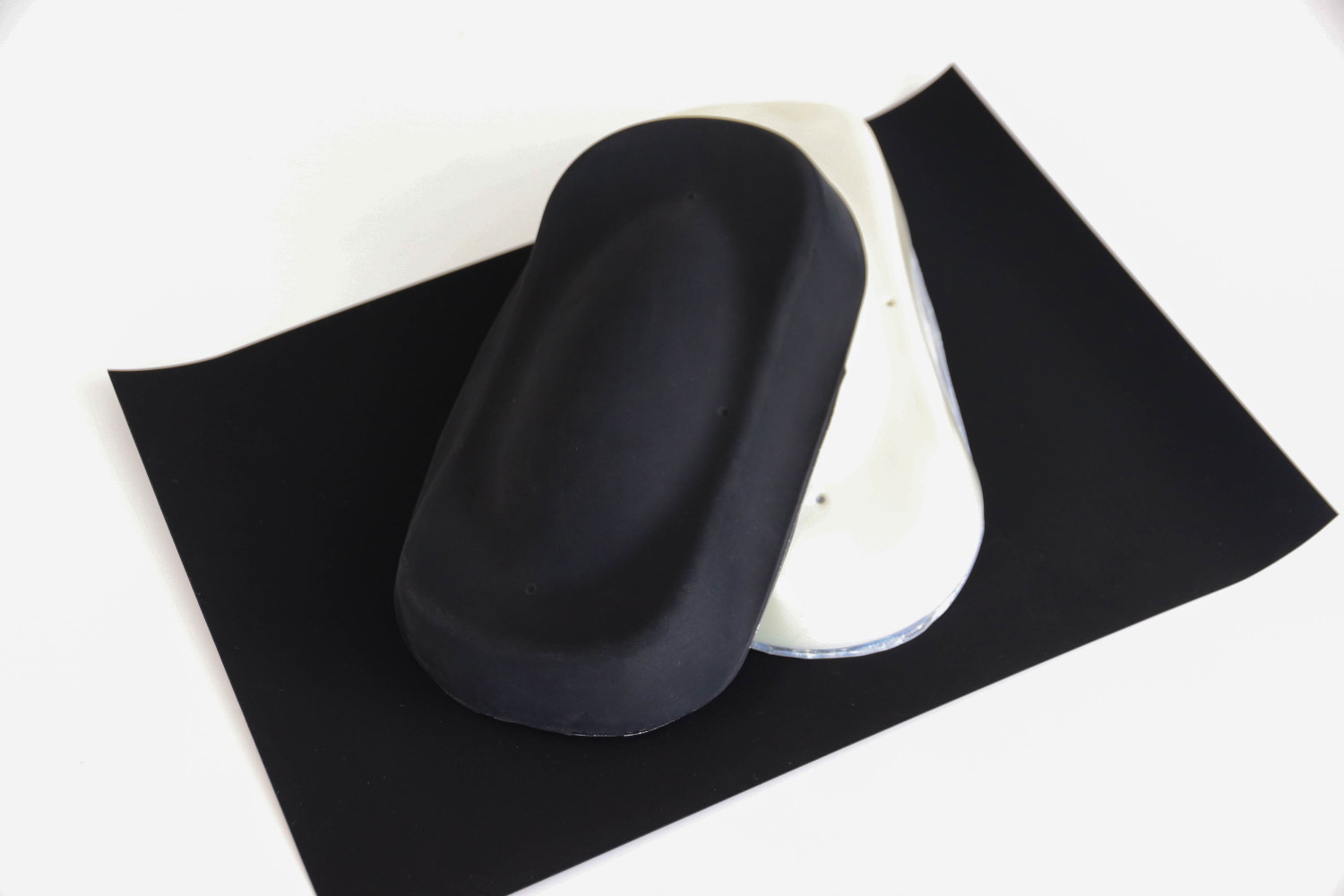